
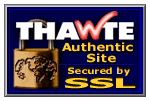
|
Inflatable Boat, Plastic Kayak, and Canoe Materials
- Inflatable Base Fabrics
- Hoop Stress and Stretch
Denier Thread Count and Tensile Strength
Weave
-
-
-
-
-
- Fabric Coatings
- Neoprene
Hypalon
PVC
Urethane
Elvaloy and Aqualoy
- Unsupported Fabric
- Kayak and Canoe Plastic materials
- Polyethylene
Royalex
- Welding Vs Gluing inflatable fabrics
- This is on a seperate web page, but I thought it would be good to mention it here.
-
Inflatable Base Fabrics
I use the term base fabric to describe the material upon which the coating is placed. If there is no base fabric I call it unsupported fabric, and is usually urethane or vinyl. The base fabric is what gives the material rip strength. and allows shapes to be made with the air structure. The Two types of base fabrics that are commonly used are Nylon, and Polyester yarns. Nylon is stronger than polyester, and Polyester does not stretch as much as Nylon. Nylon tends to absorb moisture where Polyester does not. Mildew can become a problem, and may cause coating to delaminate from a Nylon base fabric because of this tendency to absorb moisture.
Hoop Stress and Stretch
In an air structure there is a property called hoop stress. The bigger the diameter of the tube the greater the stress on the fabric for any given pressure. Therefore a small diameter tube can withstand greater pressure inside and still have the same amount of stress on the fabric. Now think about a long inflated tube. If the base fabric stretches, it will take more pressure inside of the tube to keep it ridged, because the fabric can stretch along the outside of the bend in the tube. This is why some inflatables never seem to attain the same rigidity as others. Their base fabrics are of nylon and the more ridged ones are of polyester. Polyester based inflatables do not bend as easily in the waves as do nylon based inflatables. An inflatable of polyester requires less air pressure and there is less stress on the fabric. In the welding process, stretch in the fabric is critical. We chose materials with a low stretch potential so that we can maintain the dimensions of the boat both when welding and when it is finally inflated.
A more extensive study of hoop stress can be found at this web site on Page 10. It is from the naval surface warfare center (some people we have worked with before) and these people use some sophisticated science.
Denier Thread Count and Tensile Strength
Very often the base fabrics of a material are listed by denier, and this gives customers the idea that the higher the denier the more tensile or rip strength the fabric has. In general this is true, but there are exceptions. Three factors determine the strength of a fabric. They are denier, thread count and bundle size, and weave. A one denier fabric is made of fibers that weigh one gram and are 9000 meters long. A 1000 denier fabric has fibers that weigh 1000 grams and are 9000 meters long. A 1000 denier fabric may have one fiber in a bundle, or hundreds in a bundle. If the fabric has a tight weave, then thread count per inch, or bundles per inch would be a good indicator of strength. If the fabric has a loose weave, then this may not be an accurate indication of strength. A much more accurate indicator of strength is base fabric weight. As a general rule, a material with a 13 oz base fabric per square yard will be 30% stronger than a material with a 10 oz base fabric per square yard.
Weave
There are two basic types of base fabric weaves used in the inflatable industry. One I will call conventional weave is where the thread bundles alternately pass over and under the thread bundles from the opposite direction. The other is called weft inserted weaves, and are more like a knit fabric. I am a big fan of conventional weave. Sometimes, when damaged, a weft inserted fabric will have a smaller tear, but because of the knit characteristic of the base yarn, a much larger patch has to be applied to cover the affected area. A conventional weave fabric may sustain a longer rip, but the strength of the fabric is not affected as far away from the rip as the weft inserted fabric is, and I feel this makes it easier to patch, and results in a stronger fabric.
Fabric Coatings
Fabric coatings include: neoprene, Hypalon, PVC, Urethane, Elvaloy, and Epdm. I will discuss the most popular ones, neoprene, Hypalon, PVC, and Urethane. These coatings come in two basic categories that I will call thermoplastic, and thermoset plastic. I consider Neoprene and Hypalon to be in the thermoset plastic category. If you have ever watched a tire burn, you will get an idea of what thermoset means. This is the idea that a plastic substance can bonded so tightly that it will not melt before it burns. On the other hand thermoplastics do melt readily, and can be reformed, and easily recycled. PVC, Urethane, and Elvaloy are thermoplastics.
Neoprene
Neoprene is renown for its ability to last. When I was a guide in the Grand Canyon in 1979, outfitters were still using neoprene and canvas (cotton base fabric) tubes. This material predated the invention of nylon (before 1941). The reason they failed was because the canvas would rot inside of the neoprene, and they would loose their ability to hold air pressure. The coating was still OK. Nylon was invented at the start of World War II. It is hard to find a coating that is more durable than neoprene. Neoprene is available in a cured (vulcanized) and uncured state. To cure neoprene it must be heated. Uncured neoprene will eventually cure out over time. un cured neopreme can be glued and then vulcanized in an oven (autoclave) to set a seam that is resistant to glue deteriorition. It is my opinion that Neopreme has a natural mildicide that kills the mildew that creeps in with a nylon substrate. Even so great care is usually taken to keep moisture out of nylon and neopreme boats.
Hypalon
Hypalon coatings are more chemically resistive, and have been used in applications like roofing, and secondary linings for oil tankers. Hypalon makes a very tough inflatable coating, with excellent dry abrasion qualities. There is considerable argument that it is better than neoprene. It does require a cold gluing process to build inflatables. This fabric is relatively expensive, and is more labor intensive than thermoplastic coated materials when used for manufacturing boats because the cold adheasive process is more labor intensive.. Hypalon is a trade name of the dupont corporation. Chemically it is sulphonated Polyethelene. The sulphur in the material bonds the poly very tightly, but also makes it glue-able with regular contact adheasive. Adheasives can get tired over time, and may need to be reglued. It is our oppinion that hypalon is not as UV resistant as PVC.
PVC
Also known as vinyl, is probably the most widely used coating for inflatable boats world wide. It is easy to weld, and to glue, has in my opinion the best resistance to ultraviolet radiation, and has excellent air holding properties. The dry abrasion qualities are somewhat less than Hypalon and Neoprene. However the wet abrasion qualities exceed the other two. It can be repaired with hot air welding techniques, which are faster than using adhesives. It is the least costly of all of the coated fabrics.
Urethane
Urethane coated fabrics can be engineered to have many different chemical properties. There more than 1000 different compounds of urethane. Therefore the properties can vary widely. It is generally accepted by urethane raft owners that urethane boats have better dry abrasion than PVC. I for one am not sold on this idea. Urethane melts at a considerably lower temperature than PVC. There is controversy about urethane coatings having better dry abrasion than hypalon. I do not believe that is does. Urethane is slightly more difficult to weld and glue than PVC. The cost of urethanes is high compared to PVC, making these boats more costly to construct. Urethane has the best cold crack property, and we have used both urethane/ nylon and Urethane/ polyester in pontoons that serve as shock absorbers in arctic and antarctic cargo sleds. We had many fabrics tested at the US Army cold weather research lab in New Hampshire. Urethane/ nylon was the fabric that held up the best to cold weatther and flexing.
Elvaloy and Aqualoy
Elvaloy is the trade name of a fabric that was once used by Achilles. It had great welding properties, but it was hard to glue to. Even when it is in a 10% Elvaloy to 90 % PVC base we had trouble with some of the glued parts. They needed extra care in the preparation process. Elvaloy is not widely used as of the year 2001. The Seamens corporation contiues to sell a product called XR7 fabric that is 10% elvaloy, and we understand that the chemical elvaloy is the stuff that makes the PVC soft. The Seamens company claims that unlike other pvc fabrics the Elvaloy does not migrate to the glue and weaken it. So when it is glued properly, I stays glued longer. I would like to say that this marerial welds extreemly nicely, and all air holding parts should be welded.
A note on Welding Vs Gluing:
We have been making boats by welding since 1988, and as of 2011, I do not know of a single boat that went to the land fill because a welded seam came loose. This and PVC superior uv resistance is the reason why we believe in inflatable boats from PVC. We also weld products made with urethane, and in many cases it is superior, like cold crack, or chemical resistance. It is true that Glued PVC boats may have issues with the glued components over time. However Hypalon and urethane do also. There are 2 reasons why this may seem to be a bigger problem with PVC. The same quality that makes PVC great for UV resistance compromises the glue over time. That is, the chemical used in the vinyl to keep it soft. That chemical is called Plasticizer, and over time it deteriorates the glue. Often the glue used in production in Korea and China is a 1 part adhesive that degrades easier over time. It is easier to remove the glue lines too. So it is important to use a quality 2 part adhesive, when doing permanent repairs. but welding is far superior.
Unsupported Fabrics
The term fabric is misleading in this case because there is no fabric. These materials hold air very well because there is no fabric to coat. They can be easily manufactured, usually by electronic radio frequency welding, and products are mass produced. Because there is no fabric, tensile strength is low n these products They are not recommended for serious whitewater, or motor applications.
Many manufacturers are using unsupported fabrics as a bladder inside of a coated fabric. There are some advantages to this and some disadvantages.
Advantages include: There is one more layer of material to rupture, and this may add a slight amount of security to the owner. The outer shell does not have to be air holding, and can have a heavier substrate, or a lighter substrate, or a cheaper substrate. It cost money to get fabric to hold air. In some instances a new bladder can be added and a rip sewn up to make a repair, if an owner or boatman does not know how to repair with glue or hot air welding.
Disadvantages include: The use of a zipper so that the bladder can be installed. Zippers are prone to failure over time. The accumulation of mud and moisture between the shell and the bladder. This causes the boat to become heavier, even after it is heavier to begin with. If a rip does cause the bladder to fail the bladder and the shell have to be repaired. This results in twice as much repair work. There is some loss of coating adhesion when using heavier base fabrics. This means that seams may be prone to failure, even though the rip strength of the base fabric is high.
The fabrics we use at Jacks Plastic Welding are of two weights. They both hold air very well. Our 32 oz per square yard fabric has a lighter weave, and results in a slightly lighter weight boat when used in applications where weight is a factor. Our 35 oz per square yard fabric has a much heavier weave, with good coating adhesion, and excellent tensile strength. we use this material in all of our larger craft where load capacity is the issue and strength is a bigger consideration than the weight of the boat. We also use heavier fabrics that can be installed as double bottoms on our cat tubes, and for bottom reinforcement on our self bailing rafts. In this way we build a far superior boat by using all of the best properties of these materials to the best advantage.
Kayak and Canoe Plastic Materials
Polyethylene
Polyethylene Kayaks come in two basic forms, linear and cross link. They also are manufactured by two distinct processes, blow molding, and rotationally molding. Polyethylene is a very long molecule. If lined up properly (linear) it can become dense and ridged. Cross linked polyethylene consists of long molecule chains that are linked together. Cross linking makes the material tougher by creating bonds between the molecular chains. It also makes the material harder to weld because it becomes a thermoset type of plastic.
Composite Polyethylene
Old town canoe uses a composite polyethylene. This substance has a polyethylene foam core, much like royalex has a foam core. The combination of hard skin and foam core makes a very ridged boat hull.
Royalex
Royalex is the most popular thermoplastic material used in canoe hulls. It has a ABS outside with a foam core and PVC on the inside. These materials make it very ridged, and easy to manufacture.
Top
|